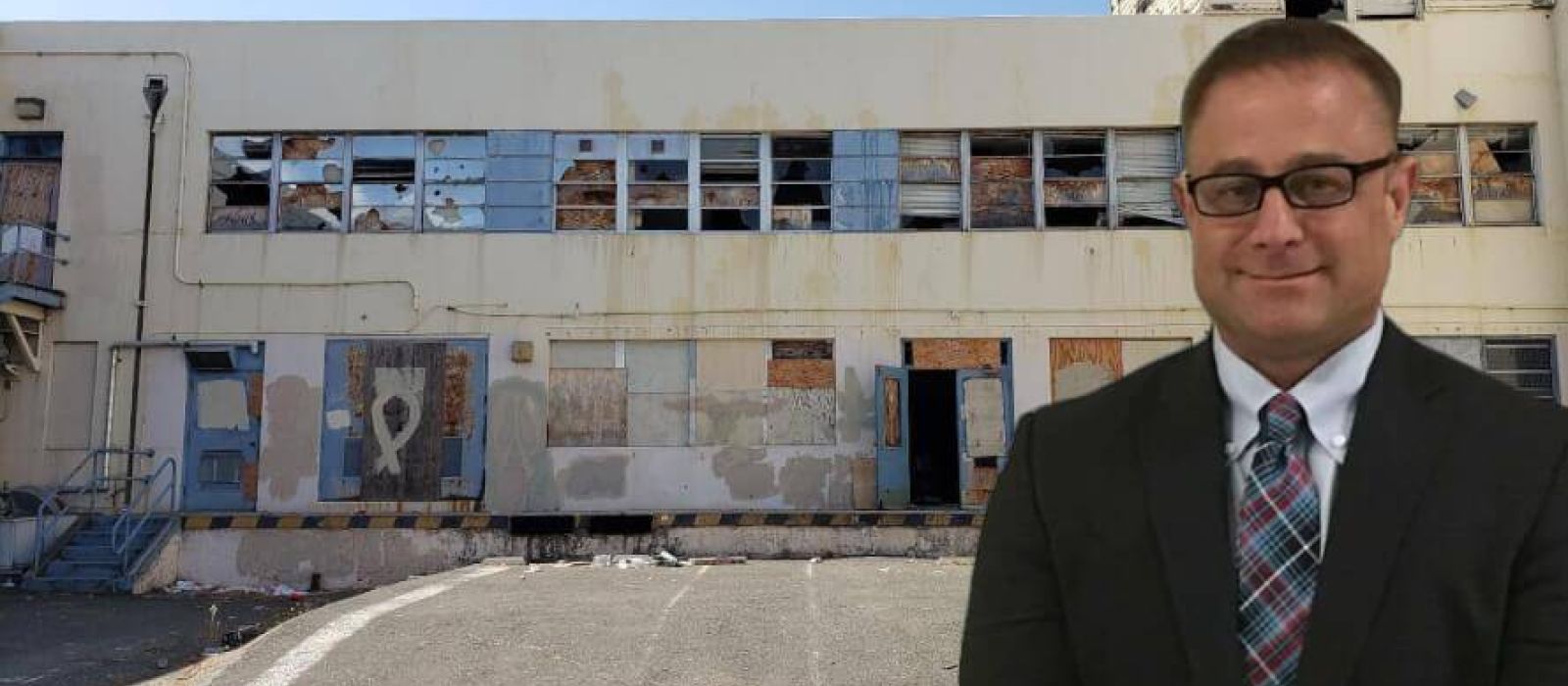
Los Angeles Truck Loading and Docking Bay Accident Attorneys
Over $150 Million Won
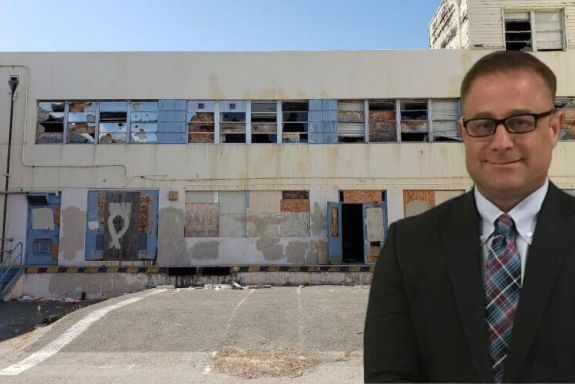
Los Angeles Truck Loading and Docking Bay Accident Attorneys
$150 Million + Won!
If we don’t win, you don’t pay.
NO WIN – NO FEE

ON CALL 24/7

U.S. Marine

Need Help For a Docking Bay Injury? Learn More Here!
I am attorney Michael Ehline. I am an expert in transportation and warehouse accidents occurring in warehouses’ Material Transfer Zones (“MTZ”). Having worked at a Home Depot while reading for the law, I am familiar with loading dock and dock plate failure mishaps. And I have litigated multiple falling overhead object cases.
I am also an expert on how these tragic events can occur. According to Safety and Health Magazine, approximately 25% of all warehouse injuries to workers and others occur during loading dock operations.
A docking bay accident injury may occur because of an accident or other incident at the warehouse’s dockyards or shipping receiving areas. The immediate aftermath of a docking bay collision can be a devastating experience. Depending on the specific injuries a person suffers during the aftermath of such an accident, some victims may sustain long-term physical injuries or even die. Before you agree to accept a settlement offer or sign any insurance paperwork concerning your injuries should consider chatting with our top California personal injury attorney about your situation. You need to ensure that you or your loved one receives adequate compensation to pay for any permanent disabilities you sustained due to the collision, including pain, suffering, or emotional injuries. Now, let’s talk about docking bay incidents.
In 2017, 270,000 transportation and warehousing industry injuries were reported, along with a whopping 819 deaths in the U.S. Only the building industry surpasses transport and warehouse killings, which recently grew 5.3% from 2016 to 2017! When you think about it, almost everything shipped from a farm, chemical or product manufacturing plant, or seaport ends at a shipping and receiving dock somewhere.
In addition to taxpayers’ costs in workers’ compensation, social security disability, and other entitlements, loading dock accidents hurt private companies. For example, some estimates say that the private industry pays out $675 million annually for packing dock-related injuries, many of which are caused by avoidable accidents. Based on statistical data, that means, on average, a work accident costs companies around $189,000 per injured worker.
Wow! The good news is that certain worker safety classes and automatic vehicle restraint devices, shown here, are proven to mitigate or eliminate severe injuries and death at warehouse loading and unloading areas. We will also discuss other common-sense ways to keep workers safe below. Of course, when these products fail, workers and families may have rights to compensation under product liability laws, reviewed here.
According to Wikipedia, a loading dock is defined as:
“… as an area of a building where goods vehicles (usually road or rail) are loaded and unloaded. They are commonly found on commercial and industrial buildings, and warehouses in particular. Loading docks may be exterior, flush with the building envelope, or fully enclosed.”
How Many Types of Loading Docks Exist in the U.S.?
There are four basic types of loading docks used for commercial truck shipping and receiving, as follows:
- Flush Dock. The most common loading dock used in transport or with heavy lifting machines, a flush port, allows the back of the loading truck to be flush against the space’s entryway.
- Open Docks
- Saw Tooth Dock
- Enclosed Dock.
In addition to my personal experiences as a warehouse worker, I have successfully represented people injured in various docking bays of all types in all classifications of wrecks. Below, I will discuss what owners, workers, and even experts need to know about these cases.
Some common hazards leading to Los Angeles loading dock accidents are:
- Poorly Marked and Maintained Floors: Slips, Trips, and Falls. Much of this malaise occurs at the edge of the dock, caused by slippery floors from grease, condensation, oil leaks, and other lousy housekeeping. These often lead to a headfirst plunge onto hard concrete or porous asphalt and gravel below.
- Poor Visibility or Lighting: In particular, bright lights should illuminate the trailer before attempting to work therein.
- Dock Separation, Early Departure, or “Trailer Creep”: A big rig sometimes lurches or rolls forward, separating the leveled trailer from the dock during loading and unloading (Forklifts and workers falling to the ground through the resulting gap are among many outcomes).
- Forklift-related mishaps include running over a worker inside the trailer, falling or overturning during a lurch event, and others.
- Backover Accidents: When a rig backs in, the trailer can crush or pin a worker against another vehicle or object. For example, someone could get pinned against a warehouse loading platform bay wall.
- Gate Crush and Pinch Accidents happen when heavy, electric-powered, or manually operated gates act as guillotines as they close.
- Diesel, Carbon Monoxide poisoning, and Lung Disease: This is due to the delivery vehicle and gas-powered powered forklifts, floor lifts, generators, and other equipment.
Enclosed loading docks are crucial for efficient shipping and receiving various agricultural and commercial products and goods from around the world during lousy weather. Because most farming machines like trucks are high off the ground, elevated warehousing docks have long been the efficient solution. Trucks back into the elevated dock open their gate, and workers can quickly roll and carry the pallets, boxes, and other items. However, accidents often happen during this process, and many cause severe and debilitating injuries to people and property.
Loading dock safety is critical in avoiding personal injuries at or near trucks and trailer staging areas. So, let’s take a look at that first. Everyone sees 18-wheeler trucks and trains on the streets and highways. Many lorries deliver goods to smaller strip malls. For example, they use a hydraulic gate lift to load and unload a few provisional goods and items like beer, pizza dough, hardware, you name it. But what about larger loads going into a warehouse? Unloading a whole truck using a tail lift would be very time-consuming. Time is money in the transportation business.
Enter the Loading Area Dock
Loading docks and loading bays are vital in efficiently operating our free market economic infrastructure. Because of this, parked trucks remain in the common rear areas of commercial and industrial buildings and warehouses as they wait for their turns. Anyone driving through the rear of a grocery store, or even Camp Pendleton’s 52 Area, has seen a loading dock. Although they come in many configurations, discussed below, I know from having “volunteered” to work at the School of Infantry’s chow hall. These bays are dangerous places for workers, lollygagging around the dock plates.
Most loading areas will have a receiving area with large metal storage shelves reaching high to their warehouses’ metal roofs. Forklifts and workers remain crucial to quick loading and offloading items for storage into the overhead bins and shelves or sent directly into the store’s merchandise overheads elsewhere. A proper General Manager or Safety Guide should orchestrate the balance between efficiency and safety during this stressful period.
Even then, a small or large object falling on a worker can cause death or severe injury. And this remains true whether the person was wearing safety protection, such as a hard hat.
Almost Half of Loading Dock Accidents Result in Death?
Yes, this appears to be the case for the reported study period. OSHA claims that from 2004 to 2014, they investigated 209 docking accidents coupled with injuries or death. Almost half of these accidents were classified as fatal. Back injuries from improper lifting or carrying are also high on the list for many warehouse workers. And people can get hurt even with hernia belts and things like mechanical lifting devices.
- Common Loading Dock Injuries Discussed in More Detail
The loading dock area must be inspected regularly to identify potential hazards, including risks for many items below.
1. Injuries Due to Ill-Equipped, Poorly Maintained, Poorly Illuminated Floors and Lack of Safety Railing
Slip, trip, and fall accidents remain common along loading docks. Some warehouses use smooth concrete flooring, adding only to weather conditions such as high humidity or rain. Due to icy or stormy conditions outside the storage facilities, truckers and laborers constantly track water, mud, and other debris.
- How Agriculture Can Cause Slips and Falls
The additional problem of vegetables and fruits falling from their bins and workers and mechanical devices tracking residue through the warehouse is no joke. Even with the best slip-resistant work boots, a worker can be hurt after slipping on a crushed-up banana, for example. Making matters worse, most large loading bays remain exposed to the elements. Since no roof protects the diesel trailer or docks in those facilities, rainwater, heavy fog, or melting snow can channel along the top into the open trailer doors and drip onto wooden flooring, making them very slippery.
And even when the docks completely enclose the trucks, their wet tires are still constantly tracking water into the loading ramps, making them slippery to a massive diesel rig and trailer. And even when ice or water is removed continuously from the floor’s surface, people still get hurt in the dock vicinity.
2. Poor Illumination
Poor lighting and inadequate handrails to grab onto add to the risks dockside workers face. As discussed, the trailer should be well-lit before anyone is allowed inside. Falling merchandise and loose or shifted loads can easily fall onto a worker, causing a crush injury or death. And a lift driver could run a worker over without proper lighting.
- Sometimes, failure to have:
Guardrails at areas where people fall can magnify the number of accidents. Even when the dock edges are marked clearly with caution symbols, the only way to go is down.
3. Dock Separation, Trailer Creep, Trailer Pop Up & Early Departure Injuries
Dangerous loading dock separation can happen in many ways. As noted above, “early departure” and “trailer creep” can kill or maim. We rank it as number two in causes of severe injury and death for our substantial warehouse injury case intake handlers. The mechanism of injury involves a truck leaving the dock prematurely. The resulting void can pull the ramp out from under a worker or forklift operator.
- Trailer Creep, also known as dock walk, happens from the repeated impact lift trucks driving in and out of the trailer. Because of this, the container will edge (“creep”) away from the dock. Wheel chocks may not do the job of stopping creep because Chocks can slip, get misplaced, or be pushed or pulled out of the way. Also, they require a fallible human to put them in place. And the result can be arguing who is at fault, the dock or the trucker.
- Early Departure or Aggressive pullout happens when a truck driver mistakenly drives away while a lift truck enters, leaves, or is still inside the trailer. Sometimes, even when proper anchors and strapping tie the container to the dock, big rigs can again creep, especially in wet conditions. As noted, trailer creep can happen when the rig is started early or not turned off during docking. And even if the rig is flush with the bay, the trailer must be LEVEL with the loading platform. Because of this, a dock leveler is used to position the trailer. However, a raised ridge or gap separation can be created if it is not perfect. Research showed that a lift truck experiences significant jarring as it encounters bumps and gaps found on standard dock levelers during the loading and unloading. Subsequent Rite-Hite studies prove that dock shock remains a substantial source of deep, repetitive vibration.
- Dock Shock and Trailer Drop are terms coined by the Rite-Hite company. They are defined as unsafe situations during the loading or unloading of semi-trailer trucks. (1) Dock shock is the jarring and jolting that occurs when a lift truck crosses between the warehouse floor and the trailer bed with different surfaces, like a stand-up walkie or a forklift. These surfaces may include concrete, wood, and metal, all relying on a ridged, metal bridge ramp or lift to get in and out of the trailer. Even though the dock is level, the vibrations can shake the snug fit away, causing someone or something to fall over. (2) Trailer drop is defined as the vertical trailer bed movement or “drop” that happens naturally as weight is removed from the trailer. Don’t forget that a forklift can weigh as many as three cars! Typically, the trailer suspension and heavy shocks can handle it. But as workers and machines go in and out, the metal ramps can jostle about and rattle themselves loose. And that can trap a foot or a toe. Also, the bumping actions can lead to chronic vibration-related injuries and possibly disc burst fracture injuries to the neck and spinal column.
- Trailer Pop-Up or Trailer Up-Ending can happen as loading or unloading occurs, and the weight of the product and the forklift cause the trailer to shift at the end or nose.
- Landing Gear Collapse, known as trailer tip-over, can happen when the landing gear legs of a human-spotted trailer collapse. The trailer may ominously tip sideways if the portion rolls in or out. However, the rotating hook vehicle restraint has been proven to hold the trailer in place so that it doesn’t fall over onto someone or another vehicle. Also, equipment under the weight of repetitive heavy loads can develop stress fractures and ultimately fail. For example, the leveling landing gear underneath trailers can give way and make a trailer violently fall over with people inside or standing nearby. So, people can be crushed to death or be maimed and in a coma from severe head injuries, even with the perfect safety record. For this reason, safety inspections must be accompanied by retrofitting and repairing continuously used machine parts.
4. Loading Dock Separation Accidents and Forklifts
The National Safety Council (“NSC”) claims $39,000 in medical costs and around $150,000 in property damage per forklift dockside accident. If you split it down the middle, that’s $75,000 in forklift repairs or replacements. Another $75,000 goes to repair structures and buildings damaged in these catastrophes. We already discussed chronic vibration injuries from dock shock. But there are also more suddenly wrought-on accidents.
For example, as the forklift driver or laborer transitions from concrete to the metal bridge and back, any gaps or spaces in the ramp and platform can topple left or right. This is a known cause of something falling into the dark, tight truck ramp. Failure to maintain a level surface is a significant cause of terrible slips and falls, leading to head, neck, ankle, knee, elbow, shoulder, and back injuries.
Manually loading or unloading a truck is always a safety challenge, requiring a quality safety program.
FACT: Yearly, 94,750 forklift-related injuries nationwide are reported. And out of this number, 7% of forklift accidents occur when a lift truck gets driven or flies off a loading bay dock. Sadly, of those figures, 70% of accidents reported were avoidable had precautionary safety measures been taken. (See also, “Towards Improved Forklift Safety Whitepaper,” www.nist.gov).
- Number One Safety Issue Preventing Death – Operator Seat Restraints
The time to put on your seat belt is not after you’ve been in a car accident. To safely drive a forklift, ensure restraints are in place and that you have eye contact with the trucker. No one should be allowed to drive off.
- Forklift Fall-Through Accidents
To recap, fatal forklift fall-throughs at loading docks often occur during loading or unloading. Sometimes, the heavy forklift’s momentum transfers to the trailer, which then extends away from the dock leveler. So you can see how dangerous that can be.
- When the Truck Driver Pulls Away Too Soon
Sometimes truckers, always on a tight schedule, believe the job is delivered, and they are clear to pull out and leave. But what happens if they are mistaken or just plain wrong? Leaving a loading dock prematurely is a known cause of many tragic forklift incidents. Imagine a truck pulling away as a forklift flies out the back, tumbling four or five feet, crashing to the asphalt.
Sometimes, forklift drivers will be ejected from the vehicle; sometimes, they are belted but try to escape a burning car. Other times the forklift driver may be trying to get away before they were crushed by the truck or another oncoming forklift that could not slow down in time to avoid falling over the side.
- Forklifts Overturning
There are many ways forklifts can overturn. First, the loadmaster or safety officer must ensure the pallets or items are light enough for the manufacturer’s load specifications. An innovative business will ensure that each worker is equipped with restraints and a safety cage. These vehicles can still flip over or fall on their side in many ways. Load shifting inside trailers and collapsing of levelers can cause a lift to fall over on its side, crushing anyone nearby, like a safety spotter. As you can see, a worker can be killed or wounded at truck docks in many ways.
Some Other Methods of Avoiding Work Injuries When Working At Docking Stations?
- Truckers and Load Masters Need to Maintain Constant Communication During Crucial Periods
Securing a trailer to the loading dock is only part of why vehicle restraints are preferred over wheel chocks. Communication between dock personnel and truck drivers is essential for maintaining safety in the loading dock, and wheel chocks do nothing in this area. Vehicle restraints often include light communication systems that know when the trailer is restrained and use interior and exterior lights to communicate to the truck driver and dock personnel so loading or unloading can safely begin.
Other Incentives to Install Restraining Devices?
- The More Safety, The Lower the Insurance Rates.
For store owners, there is also a slim chance that retrofitting restraints at your loading docks could get you lower insurance rates from your liability carrier, assuming you are not self-insured. We recommend contacting your insurance agent to find out. But either way, it’s still a business expense and well worth it.
- Is it The Law?
Many gadgets are designed to restrain a big rig and keep it still and level during load-outs. Wheel chocks have been an industry standard for generations. OSHA has specific requirements aimed at preventing trailer/dock separation accidents as follows:
1910.178(k)(1): The brakes of highway trucks shall be set and wheel chocks placed under the rear wheels to prevent the trucks from rolling while they are boarded with powered industrial trucks. 1910.178(m)(7): Brakes shall be set and wheel blocks shall be in place to prevent movement of trucks, trailers, or railroad cars while loading or unloading.
However, there are also OSHA alternatives to wheel chocks to avoid trailer separations when loading docks.
. . . in light of the changes in technology since the promulgation of 29 CFR 1910.178(k)(1) and (m)(7), OSHA as a matter of policy will regard failure to use wheel chocks or blocks as a misdemeanor violation and no citation will be issued if alternative methods of preventing truck movement are used. These alternatives may include the use of dock lock mechanisms, dock monitoring systems, or other systems which will prevent the unintentional movement of trucks and trailers while being boarded with powered industrial trucks.
As you can see, these accidents are so common and a big deal that dock personnel is required. A whole industry is designated to developing better chocks and alternative lock dock mechanisms to prevent lurching or misleveling while loading. Truckers and safety workers should all know these basic rules.
5. Backing Over Accidents
When a big-rig trucker backs up their trailer’s rear impact guard (RIG) or ICC bar, an automatic restraint typically secures the RIG to the loading dock, similar to how train cars are connected. Once disengaged, the tractor can pull the trailer away. Due to the above problems inherent in these cases, trucks are unaware there are people behind their rigs.
So, as they are being guided into the docking bays, the rig could jolt forward, causing the driver to back up, unaware of the safety person they’re trying to level the trailer with, for example. These are often fatal, especially to a child nearby, and if not, they will result in lifelong injuries.
6. Faulty Docking Bay Doors and Crushed Human Problems?
Misaligned tracks, problems with cables, spring malfunctions, and sensor issues are just some potential problems surrounding the dock doors. Like with dock levelers, having a preventative plan, rather than a reactive one, will allow you to address the problems before they become productivity-halting problems. If a worker or bystander is in the way, his fingers get trapped in the chains, or roller mechanism, amputation, peeled back flesh, head injuries, crushed limbs, and death remain common.
Pulling-away accidents are also horrific in their injury potential. Here, the truck’s towed trailer lurches back and forth, causing someone working in the back to fall into the gap between the trailer’s ramp and loading bay. It happens when the rig’s diesel engine lurches backward, crushing a limb or whole person.
7. Diesel, Carbon Monoxide poisoning, and Lung Disease?
Fumes and carbon monoxide exposure can severely harm your respiratory system over many years. Lung disease is always a potentially harmful outcome when you don’t stand up for your legal rights. Calling a personal injury lawyer will help balance your life and protect you and your family.
A Little About Commercial Truck Bays and Loading Dock Accidents
Truck bays are portals leading to and from docking bays. Other equipment is used in tandem to safely and efficiently load and unload cargo once the trucks are docked. Factors that ensure the safe function of those pieces of equipment are relative to dock door displacements from each other and adequate staging space within the facility. Bottlenecks inside and outside facilities can result from poor planning and slow workers.
Often, management did not think about providing enough space for staging. So now you may have loads, and other items staged all over the yard. And this can cause blind spots and make it harder for work machines to get around safely, which lowers productivity. Outside the loading bay, there is an area called an apron. When there is insufficient space, staged trucks can’t get in or out of the facility safely.
Due to the proximity to the trailers and rigs pulling in or out of the staging area, mirrors can get knocked off, and bicycle and motorcycle riders can be prevented from riding. Workers can also get crushed or pinched by a tractor.
Examples of Docking Bay Accidents and Injuries in Real Life:
- Day Laborer Dies when Pinned Between a Loading Dock and a Backing Track. https://www.cdph.ca.gov/Programs/CCDPHP/DEODC/OHB/FACE/CDPH%20Document%20Library/12CA009.pdf
- Dockworker Maimed After Forklift Falls Off Loading Dock. https://pinews.com/dockworker-maimed-after-forklift-falls-off-loading-dock/
- Two Maintenance Mechanics Died When a Suspended Steel Dock Plate Fell on Them. https://www.cdc.gov/niosh/face/stateface/ca/04ca013.html
- Loading Dock Accident Search OSHA: https://www.osha.gov/pls/imis/AccidentSearch.search?acc_keyword=%22Loading%20Dock%22&keyword_list=on
How To Prevent Loading Dock Hazards – What the Law Says
California Code of Regulations, Title 8 Section 3336, “Loading Dock Operations” guidelines require employers to keep trucks and trailers from driving away from loading docks until finalized loadings operation.
California Code of Regulations, Title 8, Section 3336. Loading Dock Operations states:
- Shutting off engine and engage the break while loading or unloading vehicle.
- Preventing trailer creep by using wheel chocks and vehicle restraints.
- Painting the edges of the loading dock to improve visibility.
- Providing physical barriers at dock edges when not in use.
- Ensuring dock plates have appropriate capacity, stability, and proper placement.
- Preventing employees from riding on material handling equipment.
- Posting and enforcing speed limits for industrial trucks.
- Making sure all personnel are trained in dock safety.
- Providing adequate lighting at the dock and in trailers.
- Shrink-wrapping loose product for transport or storage.
- Maintaining good housekeeping and cleaning up the area regularly.
Truckers’ Duty versus Duty of Warehouse Personnel
OSHA requires companies equipped with warehouse distribution facilities to teach workplace safety. The warehouse safety boss is tasked with choking each truck or restraining each rig with an alternative device. The trucker’s only duty is to set their brake once the vehicle is docked, set, and locked. Also, wheel chocks must be applied firmly against the wheels closest to the dock.
Otherwise, they may fail to prevent trailer creep. So this requires more than lazily throwing the chock close to trailer wheels. No, it requires elbow grease to get the chocks fitted and snug. Of course, chunks of mud, sand, rocks, ice, crushed fruits, and vegetables significantly reduce the holding power wheel chocks offer. And inattentive, lazy, shiftless truck drivers have been known to reverse drive their powerful rigs and trailers over the wheelchocks as if they weren’t even there.
No matter what, early pullaway is a threat that the dockmaster must control. Evaluating and developing operating procedures to increase general awareness, providing employee training, and enforcing safety practices can improve loading dock safety (Source).
What Do Warehouse Workers Do When Injured?
So, most laborers at loading docks are worrisome about their financial futures. Many have records or are too old and not educated enough [in their minds] to do better for themselves. Warehouse conglomerates realize there is a high risk of on-the-job injuries. However, many supervisors recognize that workers are subservient to the company out of fear.
Even when disabled from previous accidents, these injured workers on light duty are forced under duress. In other words, bosses make disabled workers continue working on ladders and up in the racks. Many will still be using large machines and equipment while trucks are moving all around beneath, knowing an accident can happen again at any time.
And even though employers are supposed to ensure high safety standards exist for the work environment, many companies place profits over people when minimizing loading bay injuries. As proactive as companies pretend to be, employees and workers can get badly hurt or killed instantly. And this is when work comp insurance kicks in to help.
But it would help if you had a decent lawyer to navigate the legal landmines associated with this complex and confusing area of employment law. Workers ‘ compensation supposedly covers many items because it is a no-fault insurance program. But you need a trustworthy lawyer who can dedicate their efforts to getting you money from more than work comp coverage.
What are the Most Common Injuries In Loading Bay Mishaps?
We help victims of a docking bay accident that caused the following injuries:
- Burns and Disfigurement.
- Wrongful Death.
- Brain Injuries.
- Amputations.
- Lacerations.
- Blindness.
- Deafness.
- Deglove.
As discussed, there are almost always other liable parties to contribute to the money pot for things like:
- Wrongful killing or death of a close family member.
- Past, present, and future lost employment wages.
- Past, present, and future pain and suffering.
- One-time, present, and future medical expenses.
- Money to cover permanent disabilities.
Most of all, once you need a loading bay accident attorney, valuable time to protect the statute of limitations will have already passed most of the time. The good news is we act quickly to preserve evidence and get your case documented for a win. So once you sign the attorney-client retainer, we immediately take action.
After that, we stay in constant contact and attend to assist in the most complex aspects of your legal case. That means we spend money to do an exhaustive case investigation. That way, we can ensure you get the maximum allowance under California negligence and worker’s compensation laws. Most of all, we fight like Marines to bring you the total compensation under the law for your tragic personal injuries.
Recap – Ehline Law Firm Personal Injury Attorneys, APLC Help With the Following Loading Bay Accident Cases.
- Hazardous and toxic chemical exposure from fumes, gasses, and chemicals.
- Forklift, dock plate, dock leveler, and pallet jack mishaps.
- Truck backup accidents and running people over.
- Pallet loads are falling or tipping over.
- Slips, Trips, and falls.
Schedule a Free Case Review With a Truck Docking Bay Accident Attorney in Los Angeles
Were you or a loved one seriously harmed during the docking process to deliver goods and things? If so, we offer a free initial personal injury case consultation so you can speak with a credible and honest lawyer. That way, you can get an opinion about your case from a personal injury lawyer in Los Angeles, California. So call Ehline Law Firm Personal Injury Attorneys, APLC, before it’s too late to protect your legal rights to receive adequate compensation.
Call (213) 596-9642 now, or use our convenient online contact us form. We have convenient physical locations in Torrance, Downtown Los Angeles, California, and meeting places up and down the California Coast. And we come to you if need be. No matter what, we make it happen! Se Habla Español! Contact us on our website form too!